Komposit af keramisk fiber

Foto: MT Aerospace , Augsburg
Keramiske fiberkompositmaterialer er en klasse af materialer inden for gruppen af kompositmaterialer eller teknisk keramik . De er kendetegnet ved en matrix af normal keramik indlejret mellem lange fibre , som forstærkes af keramiske fibre og således bliver fiberarmeret keramik , kompositkeramik eller simpelthen fiberkeramik . I den tyske specialiserede litteratur omtales materialeklassen ofte på engelsk som Ceramic Matrix Composites og forkortes CMC . Matrixen og fibrene kan i princippet bestå af alle kendte keramiske materialer, hvor kulstof også behandles som et keramisk materiale i denne sammenhæng .
Artiklen beskriver den aktuelt industrielt tilgængelige kompositkeramik med deres vigtigste fremstillingsprocesser, væsentlige egenskaber samt nogle udviklinger og vellykkede anvendelseseksempler på denne relativt unge gruppe af materialer.
introduktion
I udvikling og anvendelse af komposit keramisk øjeblikket kommer primært kul og såkaldte siliciumcarbidfibre fibre til anvendelse og i mindre grad fibre af aluminiumoxid (Al 2 O 3 ) eller blandede krystaller af aluminiumoxid og silica (SiO 2 ), såkaldt mullit , består. De vigtigste matrixmaterialer, der i øjeblikket anvendes i tekniske applikationer, er aluminiumoxid, mullit, kulstof og siliciumcarbid ( Lit .: W. Krenkel, 2003).
Motivationen for at udvikle disse keramikker stammer fra de problemer, der opstod ved anvendelse af konventionel teknisk keramik som aluminiumoxid , siliciumcarbid, aluminiumnitrid , siliciumnitrid eller zirconium (IV) oxid : alle disse materialer bryder let under mekaniske eller termomekaniske belastninger, de er i sig selv Små fabrikationsfejl eller ridser på overfladen kan blive udgangspunktet for en revne. I modsætning til metaller (nøgleord: duktilitet ), men svarer til glas, er der kun meget lidt modstand mod spredning . Det er kendetegnet ved en skør brudadfærd, der gør mange applikationer vanskelige eller umulige. Udviklingen til at forbedre denne egenskab ved at indlejre fremmede partikler, monokrystallinske korte fibre (såkaldte whiskers ) eller skiver (såkaldte blodplader ) i keramikken har kun været i stand til at forbedre deres revnebestandighed i begrænset omfang, men er blevet brugt i nogle keramiske skæreværktøjer . Kun brugen af lange fibre til at forstærke keramik var i stand til drastisk at øge denne revnebestandighed og føre til forbedrede egenskaber såsom øget duktilitet , brudstyrke og modstandsdygtighed over for termisk stød , hvormed nye anvendelsesområder kunne og kan åbnes.
Den sammensatte keramik, der produceres på denne måde, forkortes normalt i form af ”fibertype / matrixtype”. For eksempel står "C / C" for kulfiberforstærket kulstof eller "C / SiC" for kulfiberforstærket siliciumcarbid. Hvis fremstillingsprocessen skal medtages i denne forkortelse, forkortes den ofte (og også i den følgende artikel) til "fremstillingsproces-fibertype / matrixtype". For eksempel kaldes et kulfiberforstærket siliciumcarbid fremstillet ved hjælp af den flydende polymerinfiltrationsproces (se nedenfor) simpelthen ”LPI-C / SiC”.
De vigtigste fiberarmerede keramikker, der i øjeblikket er tilgængelige industrielt, er C / C, C / SiC, SiC / SiC og Al 2 O 3 / Al 2 O 3 . De adskiller sig fra konventionel teknisk keramik hovedsageligt i egenskaberne præsenteret mere detaljeret nedenfor:
- højere brudforlængelse på op til en procent
- signifikant højere revnebestandighed
- ekstrem modstand mod termisk stød
- bedre dynamisk modstandsdygtighed
- anisotrope egenskaber baseret på fiberorienteringen
historie
Der er flere tilgange til behandling af CMC'er ved hjælp af flydende, gasformige eller faste udgangsmaterialer. Teknikken med kemisk gasfaseinfiltration (CVI) fremmede udviklingen af CMC'er. CVI-teknikken er blevet undersøgt som en udvidelse af Chemical Vapor Deposition (CVD) teknologi siden 1960'erne. CVD involverer aflejring af et fast stof på et opvarmet substrat fra luftformige forløbere. Det er blevet brugt til at fremstille slidbestandige belægninger, belægninger til nukleart brændstof, tynde film til elektroniske kredsløb, keramiske fibre osv. I mange år. Når CVD-teknikken anvendes til at imprægnere relativt store mængder matrixmaterialer i fibrøse præforme, kaldes det CVI. CVI blev først brugt til at fremstille carbon-carbon-kompositter ved pyrolyse af methan ved 1000-2000 ° C. Kulstof-kulstof (C / C) kompositter har flere fordelagtige egenskaber (f.eks. Såsom lav densitet og gode mekaniske egenskaber ved høje temperaturer). Omkring 1973 blev det imidlertid tydeligt, at anvendelser af C / C-kompositter ville være begrænsede på grund af deres dårlige oxidationsmodstand ved temperaturer over 450 ° C. SiC-matrixkompositter blev betragtet som en løsning til afhjælpning af den ovennævnte mangel på C / C-kompositter i lang levetid ved forhøjede temperaturer i oxidativt miljø. De fiberarmerede CMC'er fulgte udviklingen af C / C-kompositter og CVI-produktionsteknologi. CVI SiC / SiC kompositudvikling begyndte i 1980'erne, da SEP (nu SNECMA ), Amercorm , Ildfaste kompositter og andre begyndte at tilføje udstyr og processer til fremstilling af CMC-komponenter til luftfarts-, forsvar- og andre applikationer. SNECMA var i spidsen for denne teknologi og demonstrerede forskellige CVI-SiC / SiC-komponenter med tilfredsstillende ydelse på turbinemotorer. En række CVI-SiC / SiC-komponenter har vist sig at være vellykkede inden for turbinemotorer og andre komponenter. Gennemførligheden af CVI-SiC matrixkompositter blev undersøgt i 1977 og uafhængigt bekræftet i 1978. CVI SiC-matrixkompositter forstærket med SiC-fibre er fremstillet siden slutningen af 1980'erne. Nuværende CVI SiC / SiC-kompositter har fremragende ydeevne under ekstreme forhold, såsom forhøjede temperaturer. I mellemtiden er der udviklet alternative fremstillingsprocesser såsom smelteinfiltration (MI), polymerinfiltration og pyrolyse (PIP) og hybridmetoder, der kombinerer CVI og andre metoder. Der har været enorme fremskridt i CMC-udviklingen i løbet af de sidste 30 år.
Fremstilling generelt
Produktionen af komponenter fremstillet af fiberarmeret keramik foregår normalt i tre trin:
- Arkivering og fastgørelse af fibrene i den ønskede komponentform
- Introduktion af det keramiske matrixmateriale mellem fibrene
- Efterbehandling og om nødvendigt yderligere efterbehandlingstrin, såsom påføring af overtræk
Det første og sidste trin er næsten det samme for alle typer fiberarmeret keramik:
I det første trin lægges fibrene (teknisk også kaldet rovings ) ned og fastgøres ved hjælp af forskellige teknikker, der ligner produktionen af fiberarmeret plast : nedlæggelse af fiberstoffer , vikling, fletning eller strikning af fibre er eksempler på dette. I det tredje og sidste trin er konventionel slibning , boring , lapping eller formalingsteknik almindelig, som det er tilfældet med al keramik med diamantværktøj. På grund af de særlige egenskaber ved den fiberarmerede keramik er behandlingsteknikker med vandstrålen og laseren også mulige uden problemer.
Det andet trin kender i øjeblikket i princippet fem forskellige metoder til at bringe den keramiske matrix mellem fibrene:
- Afsætning af keramik fra en varm gasblanding
- Generation ved pyrolyse indeholdende en Si og C-atomer polymer
- Generering gennem kemisk reaktion
- Generering ved sintring ved lave temperaturer (1000 til 1200 ° C)
- Generering ved elektroforese med keramisk pulver
Den femte metode er endnu ikke i industriel brug. For alle de nævnte processer er der også undervarianter, der adskiller sig i procesrelaterede detaljer såvel som kombinationer. De findes i bøger, specialtidsskrifter og kongreslitteratur. De er kun beskrevet i forenklet form nedenfor.
De første tre processer anvendes næsten udelukkende til produktion af ikke-oxid, den fjerde til produktion af oxidkompositkeramik.
Fælles for alle metoderne er, at fremstillingsprocessen, som forklaret nedenfor, fører til et porøst materiale.
Bemærkninger om keramiske fibre
Blandt de keramiske fibre er ikke kun fibre associeret med fiberarmeret keramik, forstået, at ligesom ægte teknisk keramik omfatter en polykrystallinsk materialestruktur, men også dem, der har et amorft arrangement af atomer. På grund af den høje temperatur i fremstillingen af kompositkeramik er brugen af ikke kun organiske, men også uorganiske metal- og glasfibre udelukket. Kun stabile keramiske fibre ved høj temperatur lavet af krystallinsk aluminiumoxid , mullit (blandede krystaller af aluminiumoxid og siliciumoxid), stort set krystallinsk siliciumcarbid og zirconiumoxid, carbonfibre med de grafitiske lameller i retning af fibrene og amorfe fibre fremstillet af siliciumcarbid anvendes i applikationer. Alle disse "keramiske" fibre er kendetegnet ved en strækbarhed, som ved over 2% i nogle tilfælde er væsentligt højere end strækbarheden af normal keramik (ca. 0,05 til 0,10%). Årsagen til dette er, at fibrene, afhængigt af producenten, indeholder forskellige tilsætningsstoffer (f.eks. Ilt, titanium, aluminium, se keramisk fiber ), uden hvilke de amorfe SiC-fibre f.eks. Aldrig har en strækbarhed på 2% og en trækstyrke styrke på over 3000 MPa kunne opnå. Med disse egenskaber kan fibrene også være to- og tredimensionelle fiberstrukturer vævet (se figur). Ved bearbejdning, f.eks. Ved vævning, skal fibrene modstå høje trækbelastninger og små bøjningsradier.
Produktion i detaljer
Afsætning af matrixen fra en gasblanding
Denne proces er afledt af belægningsprocesser, hvor en bestemt gas eller gasblanding afsætter materiale på opvarmede overflader. Det kaldes CVD-processen ; CVD er en forkortelse for Chemical Vapor Deposition .
Når denne proces påføres en fiberstruktur, der er fikseret i form af en komponent, afsættes belægningsmaterialet også på fiberoverfladerne inde i komponenten. Derfor er denne metode også kendt som kemisk dampinfiltration (henholdsvis engl. Kemisk dampinfiltration eller CVI-metode ).
Et eksempel på dette er en fremgangsmåde til fremstilling af C / C: en C fiberstruktur produceres under visse tryk (sædvanligvis under 100 hPa) og temperaturforhold (sædvanligvis over 1000 ° C) med en blanding af argon og methan (CH 4 ) eller propan (C 3 H 8 ). Fra gasblandingen afsættes kulstof på og mellem fibrene.
Et andet eksempel er aflejring af siliciumcarbid. En gasblanding af hydrogen som en katalysator og methyl trichlorsilan (MTS, kemisk formel CH 3 SiCl 3 ), som også spiller en rolle ved fremstilling af siliconer , er normalt bruges til dette formål . Carbon- og siliciumatomerne i MTS-molekylet danner siliciumcarbid på en hvilken som helst overflade med en temperatur på over 800 ° C, de andre H- og Cl-atomer forlader processen som HCI- gas sammen med hydrogenet.
Under afsætningen oprettes uundgåeligt lukkede porer, når gasindgangsåbningerne er vokset.
Matrixgenerering ved pyrolyse af C- og Si-holdige polymerer
Egnede polymerer fremstillet af carbonhydrider danner kulstof under pyrolyse med volumenkrympning og udgasning. Polymerer, hvor nogle af carbonatomer er blevet erstattet af siliciumatomer, for eksempel såkaldte carbosilaner , danner ligeledes et amorft og hovedsageligt carbonberiget siliciumcarbid under pyrolyse, ligeledes med volumenkrympning og udgasning .
Fibre, fiberstoffer eller stakke af fiberstoffer og også tredimensionelle fiberstrukturer kan gennemblødes eller infiltreres med disse polymerer. Efterfølgende hærdning og pyrolyse fastgør strukturen i et første trin. På grund af volumenkrympningen har matrixen stadig en høj porøsitet på dette trin, hvilket ikke er acceptabelt for de fleste applikationer. For at reducere porøsiteten kræves derfor normalt fem til otte efterfølgende cyklusser med imprægnering , hærdning og pyrolyse for at fuldføre den strukturelle komponent.
Processen kaldes for det meste flydende polymerinfiltrering, forkortet til LPI-proces , og undertiden også som polymerinfiltrering og pyrolyse, forkortet til PIP-proces .
Også her er der resterende porøsitet, da hver polymer krymper i volumen under pyrolyse. Porøsiteten reduceres med hver infiltrations- og pyrolysecyklus.
Matrixgenerering gennem kemisk reaktion
I denne proces er der allerede et materiale til stede mellem fibrene, der omdannes til den ønskede keramiske matrix gennem kemisk reaktion med et andet stof. Produktionen af konventionel keramik bruger også sådanne reaktioner: Reaktionsbundet siliciumnitrid (RBSN) produceres ved omsætning af siliciumpulver med nitrogen, og porøst carbon omdannes til silicium til dannelse af siliciumholdigt siliciumcarbid , såkaldt SiSiC .
Et eksempel på produktionen af fiberarmeret keramik med denne proces er den såkaldte rettet smelteinfiltration: smeltet aluminium mellem fibrene oxideres ved optagelse af ilt til aluminiumoxidmatricen. Legeringskomponenter i smelten forhindrer den kontinuerlige oxidation i at blive afbrudt ved dannelsen af aluminiumoxidbarrierer. Det færdige materiale indeholder stadig resterende komponenter af ureageret aluminium.
Et andet eksempel, der er blevet introduceret industrielt til fremstilling af keramiske bremseskiver, er omdannelsen af matrixcarbonet af et porøst C / C-materiale med flydende silicium. Med kontrolleret processtyring under vakuum og over siliciumets smeltetemperatur (1410 ° C) reagerer matrixcarbonet i det væsentlige for at danne siliciumcarbid, og fibrene forbliver næsten upåvirket og kan således udføre deres forstærkningsfunktion. Denne proces kaldes normalt Liquid Silicon Infiltration, eller kort sagt LSI-processen .
I disse processer er den tilbageværende porøsitet så lav som mindre end 3%.
Matrixgenerering ved sintring
I oxidkompositkeramik produceres matrixmaterialet i øjeblikket af primære materialer ved højtemperaturbehandling ("sintring"). Disse råmaterialer gør det muligt at holde temperaturerne lavere end de sædvanlige sintringstemperaturer for konventionel keramik, som er omkring 1600 ° C. De tilgængelige oxidfibre ville blive beskadiget for meget af så høje temperaturer. De primære materialer er væsker, der blandes med mere eller mindre høje andele af oxidiske keramiske pulvere til dannelse af en såkaldt slip og derefter føres ind i fibrene. Ved temperaturer mellem 1000 og 1200 ° C dannes den oxidkeramiske, porøse matrix (forbundet med stærk volumenkrympning). Et eksempel på materialerne er blandinger af Al 2 O 3 pulver med tetra-ethyl-ortho silicat , der (både silicium og oxygen-donor) og aluminium butylat (som aluminium donorer) i den korrekte blanding af mullit produkter som en matrix . Sol-gel- fremgangsmåder bør også nævnes som yderligere muligheder for væskerne . Imidlertid er den kendte teknik rent vandige suspensioner af pulvere med nanometer-kornstørrelser, hvori en andel af grovere oxidkeramiske pulvere af forskellig kvalitet (aluminiumoxid, zirconiumoxid) tilsættes.
Her er porøsiteten af kommercielt anvendt materiale omkring 20%.
Matrixgenerering ved elektroforese
I elektroforese , dispergeret , elektrisk ladede partikler i en væske er transporteret til den modsat ladede overflade og aflejres der i det elektriske jævnspændingsfeltet af to elektroder . Hvis der anvendes en fiberstruktur som overfladen, aflejres pulverpartiklerne der og fylder også mellemrummene mellem fibrene. Fiberforstærket keramik produceret på denne måde er i øjeblikket ikke i industriel brug. Problemer inkluderer den relativt komplekse forberedelse og dispersion af pulveret, indstilling af ladning og begrænsning til meget tynde komponentvægtykkelser.
Permanent porøsitet skabes også her ved overvækst af adgangskanaler.
egenskaber
Mekaniske egenskaber
Grundlæggende mekanisme for mekaniske egenskaber
Forøgelsen i revnebestandighed nævnt i indledningen ved at indlejre keramiske fibre i den keramiske matrix er baseret på følgende grundlæggende mekanisme:
Når det læsses, danner matrixmaterialet revner ligesom i den uforstærkede form, når det strækkes over (afhængigt af matrixtypen) 0,05%, og de indlejrede fibre danner en bro over revnen. Denne bromekanisme kræver, at matrixen kan glide langs fibrene, dvs. at den kun er svagt mekanisk forbundet med fibrene. Med en fast forbindelse mellem matrixen og fibrene skal fibrene i broen have ekstrem høj strækbarhed eller tilsvarende lav stivhed, men dette er ikke tilfældet. Dette betyder, at matrix revnen også vil gå gennem fibrene på samme punkt med en fast forbindelse, og den fiberforstærkede keramik viste den sprøde brudopførsel af den ikke-forstærkede keramik.
Hemmeligheden bag fiberarmeret keramik med høj revnebestandighed er derfor at sikre under fremstillingen, at forbindelsen mellem fibrene og matricen muliggør glidning. Kun på denne måde kan fibrene udgør en væsentlig bro over revner og bringe deres strækbarhed (mere end 2% for C og SiC fibre, næsten 1% for Al 2 O 3 fibre). Ved fremstilling af fiberarmeret keramik sikres denne glidemekanisme normalt ved en tynd belægning af fibrene med carbon eller bornitrid . Disse belægninger har atomært arrangerede, lamellære glideplaner og danner smøremidlet mellem fibrene og matricen.
Oxidkompositkeramik har et særligt træk: Den svage forbindelse er skabt af matrixens høje porøsitet eller af kunstigt skabte mellemrum mellem fiberen og matrixen. Sidstnævnte kan fx opnås ved en hvilken som helst belægning på fibrene, for eksempel med kulstof, som brænder ud under den sidste sintringsproces og efterlader et tilsvarende hul. Imidlertid fører en for høj matrixporøsitet til lave tryk- og bøjningsstyrker, således at der i praksis skal findes et kompromis mellem gode styrkeværdier og god brudadfærd.
Egenskaber til træk- og bøjningsbelastninger, revneresistens
Fiberbelægningens indflydelse på egenskaberne af sådan sammensat keramik bliver synlig ved bestemmelsen af bøjningsstyrke , trækstyrke og revnebestandighed på materialeprøver.

Billedtekst: SiSiC: konventionel SiSiC , SiCSiC (CVI) og CSiC (CVI): SiC / SiC eller C / SiC, CSiC (95) og CSiC (93): i LPI-processen produceret C / SiC, Ox (PP): oxidkompositkeramik, CSiC (Si): C / SiC produceret i LSI-processen.
Kurverne for målinger af revnebestandighed på udskårne prøver er vist som et eksempel på billedet til højre. I disse tests lægges der med stigende kraft et hakket prøve (se billede), indtil det går i stykker. Kraften og stien til det kraftindførende hul måles. I brudmekanik normaliseres kraften til stressintensitetsfaktoren (SIF, kendt i teknologien som K 1c- faktoren) under hensyntagen til størrelsen på den resulterende brudoverflade. Da det viste sig, at størrelsen af brudoverfladen i kompositkeramik ikke kan bestemmes, normaliseres de viste kurver kun til størrelsen på det indledende hak og betegnes derfor også som den formelle SIF "K" i figuren . Da denne værdi svarer til en kraft, kan arealet ( integralet ) under kurverne i en relativ sammenligning af kurverne med hinanden betragtes som den energi, der skal bruges til at ødelægge prøven. Resultaterne er kun direkte sammenlignelige, hvis prøvegeometrien er identisk for alle prøver.
Krakningsmodstandskurverne for de forskellige kompositkeramikker vist på billedet viser, at det specifikke energiforbrug, hvormed en revne kan drives gennem kompositkeramiske prøver, er mange gange så meget som konventionel SiSiC-keramik. Det maksimale af de forskellige revnebestandighedskurver indikerer det krævede niveau, der kræves for at drive revnen gennem prøven. Forskellige typer og fremstillingsprocesser fører til genkendelige og klare forskelle i kvaliteten af denne materialeklasse, især med hensyn til revnebestandighed.
Materiale type | Al 2 O 3 / Al 2 O 3 | Al 2 O 3 | CVI-C / SiC | LPI-C / SiC | LSI-C / SiC | SSiC |
---|---|---|---|---|---|---|
Porøsitet (%) | 25 | <1 | 12. | 12. | 3 | <1 |
Massefylde (g / cm³) | 2.8 | 3.9 | 2.1 | 1.9 | 1.9 | 3.1 |
Trækstyrke (MPa) | 170 | 250 | 310 | 250 | 190 | 200 |
Brudforlængelse (%) | 0,3 | 0,1 | 0,75 | 0,5 | 0,35 | 0,05 |
Elasticitetsmodul (GPa) | 100 | 400 | 95 | 65 | 60 | 395 |
Bøjningsstyrke (MPa) | 350 | 450 | 475 | 500 | 300 | 400 |
Forklaringer til tabellen: Præfikset CVI-, LPI- og LSI- henviser til fremstillingsprocessen for den respektive C / SiC-kompositkeramik. Dataene for kompositkeramikken kommer fra ( Lit .: W. Krenkel, s. 143), dataene for oxidkompositkeramikken Al 2 O 3 fra Pritzkow Spezialkeramik og dataene for SSiC fra et datablad fra HCStarck Ceramics. Trækstyrken for SSIC og Al 2 O 3 blev beregnet ud fra brudforlængelse og elasticitetsmodul , eftersom trækstyrker er ikke specificeret for konventionelle keramik , men normalt kun bøjningsstyrke- værdier . Det skal bemærkes, at dette er gennemsnitsværdier. Inden for de enkelte fremstillingsprocesser, herunder konventionel keramik, er der undertiden betydelige afvigelser fra de specificerede værdier.
Når man tester trækstyrken af kompositkeramik, i modsætning til konventionel keramik, skyldes kvasi-plastikkurver og mulige forlængelser på op til en procent, mere end ti gange elasticiteten af al teknisk keramik , af revnedannelsesmekanismen ; kvasiplastik, fordi kurven, der drejer efter det lineære-elastiske område, ikke er baseret på plastisk deformation af materialet, men skyldes dannelsen af et revnesystem, der holdes sammen af fibrene. Da de bærende fibre har et mindre elasticitetsmodul, falder kurvens hældning og simulerer således plastisk adfærd. Også her viser værdierne i tabellen, at de forskellige typer kompositkeramik bruger fiberudvidelsen i forskellige grader.
Målekurverne til bestemmelse af bøjningsstyrken ser praktisk talt ud som kurverne vist ovenfor til bestemmelse af revnebestandighed. Ved vurdering af træk- og bøjningsstyrker skal der sondres mellem to ting:
- Materiale med ringe eller i ekstreme tilfælde ingen matrix har høj trækstyrke (nemlig fibertrækstyrke), men praktisk talt ingen bøjningsstyrke.
- Omvendt viser materiale med et højt matrixindhold og lav porøsitet høje bøjningsstyrker (som konventionel keramik), som igen ikke siger noget om, hvorvidt fibrene anvendes.
Begge værdier skal ses uafhængigt af hinanden.
Andre mekaniske egenskaber
I mange komponenter lavet af kompositkeramik er fibrene i todimensional form enten som stablede stoflag eller som krydsede lag af endimensionelt justerede fibre. Materialerne er derfor anisotrope . Udbredelsen af revner mellem disse lag hindres ikke af nogen fiberbro. Værdierne for den interlaminære forskydningsstyrke er tilsvarende lave for dette materiale, ligesom trækstyrken vinkelret på stoffet. Som med fiberarmeret plast er mulig delaminering et svagt punkt i materialet. Det kan forbedres betydeligt ved at indføre tredimensionelle fiberstrukturer.
materiale | CVI-C / SiC | LPI-C / SiC | LSI-C / SiC | CVI-SiC / SiC |
---|---|---|---|---|
Interlaminar forskydningsstyrke (MPa) | 45 | 30. | 33 | 50 |
Trækstyrke vinkelret på fiberplanet (MPa) | 6. | 4. plads | - | 7. |
Trykstyrke vinkelret på fiberplanet (MPa) | 500 | 450 | - | 500 |
Kommentarer til tabellen: På grund af porøsiteten er trykstyrkeværdierne lavere end for konventionel keramik, hvor mere end 2000 MPa er specificeret for siliciumcarbid. Porøsitet og mangel på fiberbroer fører til de meget lave trækstyrker vinkelret på fiberplanet.
Fibrenes revnebrydende virkning gør det også muligt for denne keramik at blive udsat for høje dynamiske belastninger. Prøver udsættes for cyklisk tryk og trækbelastning, indtil de går i stykker ved skiftende belastningstest, såkaldte "lav" eller "høj cyklus træthedstest". Jo højere startbelastning, jo færre cyklusser overlever prøven. Forskellige startbelastninger plottet mod logaritmen for det respektive antal opnåede cykler resulterer i den såkaldte Wöhler-linje. Det viser, hvor mange tusinder eller millioner af belastningscyklusser, det testede materiale kan overleve under en bestemt dynamisk belastning. Fiberforstærket keramik kan komme med fremragende resultater her: Ved 80% af duktiliteten, når de udsættes for cykliske belastninger, overlever SiC / SiC omkring 8 millioner spændingskompressionscyklusser (se billede).
Den Poissons forhold viser en anomali vinkelret på todimensionale fiber plan under målingen: den forudsætter negative værdier i retningen vinkelret på fibrene, hvis, på grund af dannelsen af interlaminære revner, prøvens tykkelse forøges kortvarigt i den tidlige fase af målingen i stedet for at falde.
Termiske og elektriske egenskaber
De termiske og elektriske egenskaber ved fiberarmeret keramik er resultatet af komponenterne i fibre, matrix og porer og deres sammensætning. Fiberorienteringen genererer også retningsafhængige ( anisotrope ) parametre.
Den mest almindelige sammensatte keramik, der i øjeblikket er tilgængelig, kan opsummeres som følger:
Fiberforstærket keramik, der bruger oxider, er stadig meget gode elektriske isolatorer, og på grund af porerne er den varmeisolerende effekt betydeligt højere end konventionel oxidkeramik .
Anvendelsen af kulfibre øger den elektriske og termiske ledningsevne i retning af fibrene, så snart der er direkte elektrisk kontakt med dem.
Som en matrix er siliciumcarbid en meget god varmeledning . Som en elektrisk halvleder falder dens elektriske modstand med stigende temperatur. På grund af deres amorfe mikrostruktur leder siliciumcarbidfibre varme og elektrisk strøm meget dårligere. I kompositkeramik med siliciumcarbid som matrix falder både den termiske og elektriske ledningsevne til lavere værdier på grund af porøsiteten. Nogle af oplysningerne er anført i den følgende tabel.
materiale | CVI-C / SiC | LPI-C / SiC | LSI-C / SiC | CVI-SiC / SiC | SSiC |
---|---|---|---|---|---|
Varmeledning (p) [W / (m · K)] | 15. | 11 | 21 | 18. | > 100 |
Varmeledningsevne (r) [W / (m · K)] | 7. | 5 | 15. | 10 | > 100 |
Termisk ekspansion (p) [10 −6 · 1 / K] | 1.3 | 1.2 | 0 | 2.3 | 4. plads |
Termisk ekspansion (er) [10 −6 · 1 / K] | 3 | 4. plads | 3 | 3 | 4. plads |
specifik elektrisk Modstand (p) [Ω · cm] | - | - | - | - | 50 |
specifik elektrisk Modstand (er) [Ω · cm] | 0,4 | - | - | 5 | 50 |
Bemærkninger til bordet: Med (p) og (s) er egenskaberne p arallel og s beregnet til at enkrecht fiberorientering af det anisotrope materiale. Der er ingen litteratur eller producentoplysninger om værdier, der ikke er indtastet. På grund af sin lave porøsitet har LSI-materialet den højeste varmeledningsevne af al kompositkeramik - en fordel ved at bruge dette materiale som et stærkt belastet bremseskivemateriale. Også her kan værdierne variere betydeligt, selv inden for de enkelte keramiske typer, afhængigt af detaljerne i fremstillingsprocessen.
Normal keramik og teknisk keramik er følsomme over for termiske spændinger, som er særligt høje, når de udsættes for termiske stødbelastninger . Årsagen ligger i den lave elasticitet og høje stivhed (høj elasticitetsmodul ) af disse materialer. Temperaturforskelle i materialet frembringer forskellig ekspansion, hvilket fører til tilsvarende høje spændinger på grund af det høje elasticitetsmodul. Dette får materialet til at strække sig over og gå i stykker. I fiberforstærket keramik er sådanne revner overbygget af fibrene. En komponent lider ikke under nogen makroskopisk skade, selvom der er dannet revner i den keramiske matrix. Brugen af denne materialeklasse i skivebremser beviser ydelsen af kompositkeramik under ekstreme termiske stødforhold.
Korrosionsegenskaber
Bredere undersøgelser af korrosionsadfærd for fiberarmeret keramik er endnu ikke tilgængelige. Også her bestemmes egenskaberne af egenskaberne for de anvendte komponenter, nemlig fibre og matrix.
Generelt er keramiske materialer meget modstandsdygtige over for korrosion sammenlignet med de fleste andre materialer. Det store antal fremstillingsvarianter med forskellige tilsætningsstoffer, f.eks. Sintringshjælpemidler , blandede former, især med oxiderne, urenheder, glasfaser ved korngrænserne og forskelle i porøsitet har en afgørende indflydelse på korrosionsadfærden ( Lit .: J. Kriegesmann ).
Følgende kan ses i korte træk fra litteraturen om matrixen og fibermaterialerne, der i øjeblikket er vigtige i applikationer:
- Aluminiumoxid: I sin meget rene tilstand er
aluminiumoxid modstandsdygtig over for næsten alt; amorfe glasfaser ved korngrænserne og siliciumoxidindholdet bestemmer korrosionshastigheden i koncentrerede syrer og baser . Ved høje temperaturer fører de til krybeadfærd under belastning . Til metal smelter anvendes aluminiumoxid kun til ædle metaller som guld eller platin. - Alumina-fibre:
opfører sig på samme måde som aluminiumoxid. De kommercielt tilgængelige fibre har ikke ekstrem renhed og er derfor mere skrøbelige. Krybeopførslen ved temperaturer over ca. 1000 ° C tillader i øjeblikket kun få anvendelser af oxidkompositkeramik.
- Carbon:
Carbon korroderer, forbrænder bedre med ilt ved temperaturer fra omkring 500 ° C. Det oxiderer også i stærkt oxiderende medier (fx koncentreret salpetersyre ). I de fleste smeltede metaller opløses eller danner det carbider .
- Kulfibre:
Kulfibre opfører sig næsten som kulstof.
- Siliciumcarbid:
Meget rene varianter af siliciumcarbid er blandt de mest korrosionsbestandige materialer. Kun stærke baser, ilt fra ca. 800 ° C og de fleste metalsmeltninger reagerer med dette materiale. I smeltede metaller dannes både carbider og silicider (forbindelser af silicium med metal).
Når SiC reagerer med ilt til dannelse af SiO 2 og CO 2 , danner siliciumdioxiden et beskyttende lag, der har en passiverende virkning ("passiv oxidation"). Ved endnu højere temperaturer (fra ca. 1600 ° C) og samtidig iltmangel ( partialtryk under 50 mbar) dannes der dog ud over CO 2 og CO gasformigt siliciummonoxid (SiO), som forhindrer enhver beskyttende virkning. Denne såkaldte “aktive oxidation” fører til meget hurtig nedbrydning af siliciumcarbidet under de nævnte betingelser.
I forbindelse med kompositkeramik gælder denne karakterisering kun for SiC-matrixmateriale, der er fremstillet ved hjælp af CVI-processen. Der består matrixen af meget rent, fint krystallinsk SiC. Matrix produceret med LPI-processen er betydeligt mere følsom over for alle typer korrosion på grund af sin amorfe struktur og porøsitet. De siliciumrester, der altid er til stede i LSI-materialets matrix, resulterer i en forringet korrosionsbestandighed. - Siliciumcarbidfibre:
Da siliciumcarbidfibre produceres ved pyrolyse af tværbundne, organiske silikonsyntetiske harpikser (analogt med produktionen af carbonfibre), gælder det samme for dem som den matrix, der produceres i LPI-processen: signifikant større følsomhed over for korrosion af alkalier og oxiderende medier.
Ansøgninger
Med fiberarmeret keramik er der et materiale til rådighed, der ikke længere har de største ulemper ved konventionel teknisk keramik, nemlig deres lave brudstyrke og høje termiske stødfølsomhed. Anvendelsesudviklingen har derfor koncentreret sig om områder, hvor pålidelighed kræves ved høje temperaturer, som ikke længere er tilgængelige for metaller og under slibende (= slidfremkaldende) belastning. Følgende prioriteter er opstået i udviklingen og anvendelsen hidtil:
- Varmebeskyttelsessystemer til rumfartøjer , der udsættes for høje termiske spændinger og vibrationer, når de kommer ind i jordens atmosfære igen.
- Komponenter til gasturbiner i området med varme gasser, dvs. i turbineforbrændingskammeret , de statiske styreskovle, der styrer gasstrømmen, og de faktiske turbineblade, der driver kompressoren til gasturbinen.
- Komponenter til brænderteknologi og varme gaskanaler fremstillet af oxidkompositkeramik.
- Bremseskiver til stærkt belastede skivebremser , der udsættes for ekstreme termiske stødforhold på friktionsoverfladen (i modsætning til når en glødende del nedsænkes i vand, er der ikke noget varmeisolerende vanddamplag her).
- Komponenter til glidelejer med høj korrosions- og slidbelastning.
Derudover er alle områder af interesse, hvor der anvendes konventionel teknisk keramik, eller hvor metalliske komponenter ikke opnår en tilfredsstillende levetid på grund af korrosion eller høje temperaturer. Den følgende præsentation af nogle udviklings- og applikationseksempler er langt fra færdig og er kun beregnet til at angive bredden af de tekniske muligheder.
Udvikling til rumapplikationer
I luftfartssektoren er fiberarmeret keramik af interesse for komponenter i varmebeskyttelsessystemer og for bevægelige kontrolklapper til rumsvingere . Ved genindtræden i jordens atmosfære opstår overfladetemperaturer på over 1500 ° C på disse elementer i et par minutter, som kun kan udholdes af keramiske materialer uden større forringelse. Brug af fiberarmeret keramik til varme strukturer i rumrejser lover i modsætning til de tidligere anvendte materialesystemer blandt andet:
- Vægtbesparelser
- Et bidrag fra varmebeskyttelsessystemet til den bærende struktur
- Genanvendelighed til flere genindtastninger
Da de tilgængelige oxidfibre kryber under belastning ved disse høje temperaturer, og de amorfe SiC-fibre mister deres styrke på grund af omkrystallisation, har materialet og komponentudviklingen koncentreret sig om den sammensatte keramiske C / SiC. Den del af HERMES- programmer ESA i 1980'erne, der blev gennemført, og 1992 brudte udviklingen efter adskillige opfølgningsprogrammer, der kulminerede med udvikling og kvalifikation af næsekegle, vingeforkanter og halekontrolklapper på rumplan X-38 af NASA fundet.
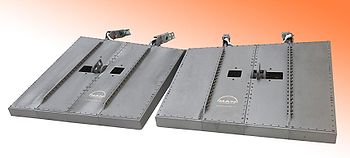
Størrelse: 1,5 × 1,5 × 0,15 m, vægt: 68 kg hver, samlet af individuelle dele med over 400 skruer / møtrikker hver lavet af CVI-C / SiC.
Foto: MT Aerospace
En af disse udviklinger tjente for eksempel til at kvalificere skruer og møtrikker fremstillet af kompositkeramik. Skruer lavet af teknisk keramik er tilgængelige, men på grund af indskæringerne i trådroden er de skrøbelige og langtfra ikke den krævede pålidelighed. Brug af skruer lavet af C / C er også for risikabelt på grund af dets følsomhed over for oxidation.
En anden vigtig komponent i disse kontrolklapper er det centralt placerede leje, gennem hvilket kraften til bevægelsen indføres. Dette leje blev testet med succes under realistiske forhold (4 tons belastning, 1600 ° C på undersiden, iltkoncentration på niveauet, når det gik ind i jordens atmosfære og samtidig 8 ° lejebevægelser med en bevægelsescyklus på fire sekunder) ved DLR i Stuttgart; fem genindtrædelsesfaser blev simuleret på denne måde.
Brugen af C / SiC har tvunget udviklingen og kvalificeringen af belægningssystemer, der forhindrer hurtig udbrænding af C-fibrene under genindgangsbetingelserne. Eksperimenter i plasmastrømmen under simulerede genindgangsbetingelser har bevist succesen med dette udviklingsarbejde.
Et yderligere kvalifikationstrin for luftdygtighed blev udført ved deformationstest ved over 1000 ° C på en IABG- teststand i München. Deformationen under en belastning på 4 tons bekræftede de tilsvarende beregninger og designet. De endelige test på jorden, efter at klapperne var blevet installeret på X-38 rumflyver i Houston, Texas, USA, beregnet til flyvetesten, var også vellykkede. Af økonomiske grunde var NASA ikke længere i stand til at nå projektets mål, nemlig transporten af X-38 med en rumfærgeflyvning i kredsløb og den efterfølgende (ubemandede) genindrejse i jordens atmosfære.
Det skal påpeges på dette tidspunkt, at disse kvalifikationer tjente brugen af C / SiC kompositkeramik til dette specielle tilfælde. Den høje temperaturbelastning varer ca. 20 minutter, når den kommer ind igen. Hvis det kan genbruges, tilføjer varigheden et par timers cyklisk belastning. Brugen af oxidationsbeskyttet C / SiC til industrielle applikationer med høj temperatur med en levetid på flere hundrede eller tusinder af timer er endnu ikke sikret.
Udvikling til brug i gasturbiner
Målet med at anvende kompositkeramik i gasturbiner er at øge gastemperaturen, hvilket fører til en øget effektivitet.
Den komplekse form af styreskovle og turbineblade i gasturbiner såvel som den meget høje termiske og mekaniske belastning på disse dele har ført til, at der oprindeligt kun blev udviklet forbrændingskamre lavet af kompositkeramik med succes . Fremskridt er kommet længst på dette område i USA. Et forbrændingskammer lavet af SiC / SiC-kompositkeramik baseret på en særlig højtemperaturbestandig SiC-fiber har været i brug i en gasturbine i over 15.000 timer. Da SiC allerede er mærkbart angrebet af oxidation ved temperaturer på omkring 1100 ° C i sådanne perioder, måtte der også udvikles en meget effektiv oxidationsbeskyttelse her. Det består af et flerlagssystem af oxidkeramik.
Det faktum, at det testede temperaturniveau endnu ikke giver nogen fordele i forhold til konventionelle metalliske forbrændingskamre, der er afkølet med en luftfilm, og at komponenterne, der følger efter forbrændingskammeret (styreskovle og turbineblade), også er udviklet og udviklet til et højere temperaturniveau forhindrer, at resultaterne hidtil implementeres hurtigt i reelle applikationer, skal kvalificeres, og at omkostningerne til produktionen af kompositmaterialesystemet fra specielle SiC-fibre, SiC-matrix og specialbelægningssystem stadig er meget høje.
Anvendelse af oxidkompositkeramik i brændere og varme gaskanaler
Iltholdige, varme gasser med en temperatur på mere end 1000 ° C fører før eller senere til brændere med konventionelle flammerør fremstillet af højtemperaturbestandigt stål til deres skalering , i tilfælde af rør fremstillet af siliciumcarbid til skade ved oxidation. Da disse dele ikke udsættes for høj mekanisk belastning, men kun for stærke termiske stød, er oxidkompositkeramik særlig velegnet til sådanne anvendelser op til 1300 ° C. Nedenstående billeder viser flammerøret til en brænder lavet af oxidisk aluminiumoxid-kompositkeramik, som er blevet brugt i 15.000 timer i en bagningslinje til knækbrød og nu har nået mere end 20.000 driftstimer. En levetid på op til 20 gange så lang som konventionelle materialer kan opnås i disse applikationer.
Klapper eller ventilatorer til regulering eller transport af iltholdige varme gasstrømme i forskellige systemer kan fremstilles af oxidkompositkeramik i samme form som metaller. De har den fordel, at de ikke deformeres (" kæde ") - lignende metaller ved temperaturer over 650 ° C. Anvendelsen af dette materiale til løft af porte (se billedserier), f.eks. I sintringsovne, som også udsættes for høje termiske belastninger på op til 1300 ° C med hyppige åbnings- og lukningsprocesser, har vist sig i et tilfælde i mere end 12 måneder med over 260.000 åbnings- og lukningscyklusser.
Anvendes som bremseskive
Ifølge bremseskiverne lavet af C / C-materiale, der længe har været i racerbiler med formlen 1 , anvendes og i bremser på fly, har nu bremseskiver fremstillet af C / SiC- materiale, som er fremstillet ved LSI-processen, kommercielt tilgængeligt og installeres i dyre sportsvogne, nogle gange mod et ekstra gebyr. LSI-processen giver fordele ved produktionen. Ruderne fremstillet af en blanding af korte fibre og harpiks presses, hærdes, pyrolyseres til dannelse af en C / C-rude og omdannes derefter som beskrevet ovenfor til en LSI-C / SiC-rude med smeltet silicium forholdsvis hurtigt og billigt.
Fordelene ved disse bremseskiver kan opsummeres som følger:
- Diskens slid er meget lavt. Levetiden sammenlignet med en konventionel grå støbejernsskive er omkring seks gange længere. Afhængigt af kørestilen tillader dette også brugen af et vindue i hele køretøjets levetid. Op til 300.000 km er specificeret under normal belastning.
- Selv under høj belastning er der ingen udsving i friktionskoefficienten , den såkaldte fadingeffekt kendt fra metalskiver .
- I modsætning til bremseskiver fremstillet af C / C, observeres ingen indflydelse af fugt på bremseevnen.
- Rudematerialet er ekstremt korrosionsbestandigt og derfor ufølsomt over for virkningen af vejsalt om vinteren.
- Massen kan reduceres til ca. 40% sammenlignet med stålskiven. På grund af den markant lavere uskærmede masse af hjulene betyder det forbedret kørekomfort og samtidig bedre greb, da hjulet lettere kan følge jordens kontur.
Da C-fibrene i vid udstrækning er beskyttet mod oxidation af SiC-matrixen, og den periode, hvor bremseskiverne kan overstige temperaturer på over 500 ° C, er begrænset til et par timer i hele køretøjets levetid, spiller oxidation af materialet en rolle i denne applikation betyder ikke noget.
Det er uvist, om produktionsomkostningerne for sådanne vinduer kan reduceres i en sådan grad, at mellemklassebiler også kan udstyres med dem. Den aktuelle status kan findes på udbydernes hjemmesider.
Anvendelser i glidelejer
Konventionel SSiC eller den billigere SiSiC er blevet brugt med stor succes i glidelejer til pumper i over 20 år ( Lit .: WJ Bartz, 2003). Lejet bruger væsken leveret af pumpen som et smøremiddel . Årsagen til succesen med dette lejekoncept er korrosionsbestandigheden over for næsten alle medier og det ekstremt lave slid forårsaget af den store hårdhed under friktionsbelastninger eller slibende belastninger fra partikler samt den lave friktionskoefficient med væskesmøring . Glidelejets SiC-komponenter består af den såkaldte akselbeskyttelsesmuffe, der er monteret på akslen og roterer i lejebøsningen. SiC-lejebøsningen er normalt krympet ned i dets metalliske miljø og er under trykbelastning . En sprød brud på denne komponent er derfor meget usandsynlig. SiC-akselbeskyttelsesbøsningen har ikke denne fordel og er derfor normalt designet med en stor vægtykkelse og / eller installeret med specielle strukturelle forholdsregler. I tilfælde af store pumper med tilsvarende store akseldiametre (100 til 300 mm) og pumper med høje lejebelastninger kunne det keramiske lejekoncept kun implementeres ved brug af kompositkeramik på grund af risikoen for svigt i beskyttelsesakselbøsningen. På testbænken kunne det vises, at lejeparringen af CVI-SiC / SiC og konventionel SSiC kan modstå næsten tre gange den specifikke lejebelastning under blandede friktionsforhold som mange andre testede parringer. Med specifik belastning er produktet af friktionskoefficienten (dimensioneløs), menes kørehastighed (m / s) og lejebelastning (MPa eller N / mm²); det angiver effekten konverteret i lejeafstanden i W / mm² og er ofte også angivet som en "P gange V-værdi", idet friktionskoefficienten udelades.
Kedelfødevandspumper i kraftværker , med hvilke der pumpes flere tusinde m³ / h varmt vand fra 160 ° C til 20 bar tryk, eller rørformede huspumper, hvormed flere ti tusind m³ / h låsevand eller havvand til afsaltning planter pumpes, har været de foretrukne anvendelser til afsaltningsanlæg siden 1994 vandsmurte glidelejer med akselbeskyttelseshylster lavet af CVI-SiC / SiC kompositkeramik (billede i begyndelsen af denne artikel).
Anvendelsen af denne type glideleje i turbopumper, med hvilke flydende ilt (flydende ilt = LOx, kogepunkt: -183 ° C) transporteres i luftfartsmotorer, er stadig under udvikling . Testene hidtil har vist:
- SiC og CVI-SiC / SiC er kompatible med LOx og reagerer ikke med ilt selv under svære forhold (for at bestemme selvantændelsestemperaturen opvarmes pulver til 525 ° C under 20 bar ren iltgas i henhold til den franske standard NF 29-763.).
- Friktionsslitestest har vist en halveret friktionskoefficient og slid reduceret til en hundrededel sammenlignet med en standard metalparring .
- LOx med smørede hydrostatiske lejer har en test et par timer med en hastighed på 10.000 min -1 med forskellige lejebelastninger og 50 Start / Stop-områder under blandede friktionsforhold overlevede praktisk taget slidfrie.
Fordelen ved disse keramiske lejer med kompositkeramik sammenlignet med lejer med konventionel keramik er den stærkt øgede pålidelighed. Beskadigelse af beskyttelsesakselbøsningen fører ikke til, at den spalter i flere større og hårde fragmenter med større følgeskader på pumpehuset og hjulet.
Andre applikationer og udviklingsmetoder
Følgende anvendelses- og udviklingseksempler kan også nævnes:
- Trykkontrolklapper i jetmotorer på kampfly , hvormed jet -tværsnittet er tilpasset motorkraften.
- CVI-SiC / SiC plader med en tredimensionel fiberstruktur som foring af varme områder af fusionsreaktorer . Den tredimensionale fiberstruktur øger varmeledningen vinkelret på pladens plan. Da krystallinsk SiC har vist sig at være et forholdsvis stabilt materiale i miljøet udsat for neutronstråling, anvendes der også her krystallinske SiC-fibre, hvis høje temperaturstabilitet er væsentligt forbedret sammenlignet med den amorfe.
- Thrustere ("finner"), flammeholdere og varme gasledningsrør i supersoniske raketter, der skal styre og afbøje ekstremt varme udstødningsgasser, i tilfælde af faste brændstoffer, også med partikler, i en kort periode på en kontrolleret måde.
- Bremseklodser til hurtig opbremsning af slæder i simuleringssystemer til ulykker i biltrafik med fordelen ved lavt slid og, selv med flere tests, meget stabile bremsedecelerationsværdier.
- Varmevekslere ved høje temperaturer med problemer med varm gaskorrosion , svarende til gasturbines, og derudover den nødvendige gastæthed.
- Stive strukturer til præcisionsspejle.
- Beklædningselementer inden for udstødningsrør fra Formel 1 racerbiler samt skiver til de tungt belastede koblinger på disse køretøjer.
Industrielle producenter i Europa
- WPX fiberkeramik: Keramiske dele og komponenter til oxidfibre til industriel varmebehandling og applikationer ved høje temperaturer
- KLETKE avancerede kompositter: Komponenter lavet af C / C, C / C med SiC-belægning ved anvendelse af C-CVI- og LSI-processer
- SGL Carbon : Bremseskiver (LSI-proces)
- Schunk Group : Aksiale lejer, radiale lejer, glideforinger, ovnforinger lavet af C / C-materiale
- BJS Keramik: luftfartskomponenter, glidelejekomponenter (CVI-proces)
- Snecma : Komponenter til rumrejser, forsvarsteknologi, bremseskiver (CVI-proces)
- Brembo : bremseskiver (LSI-proces)
- Pritzkow specialkeramik: Højtemperaturbestandige komponenter til industrielle behov lavet af oxidkompositkeramik
- CERAFIB GmbH: Høj temperaturbestandige filamenter og materialer
Forskningsinstitutioner i Tyskland
- Bremen Universitet : Institut for Keramiske Materialer og Komponenter og Biokeramik
- University of Stuttgart : Institute for Manufacturing Technology of Ceramic Components (IFKB)
- University of Karlsruhe : Institut for Keramik i Mekanik (IKM)
- Dresden : Fraunhofer Institute for Ceramic Technologies and Systems ( IKTS ) samt Institute for Lightweight Construction and Polymer Technology (ILK) ved TU Dresden
- University of Bayreuth : formand for keramiske materialer ved Institut for Materialeforskning (IMA)
- Institut for Tekstilkemi og menneskeskabte fibre (ITCF Denkendorf): fiberforskning og -udvikling
- DLR Institute of Construction and Structural Technology: Udvikling af skræddersyede CMC-materialer, f.eks. B. Termiske beskyttelsessystemer
- Fraunhofer Center for High Temperature Lightweight Construction (HTL): Forskning og udvikling af keramiske matrixkompositter (CMC), keramiske fibre og højtydende keramik
litteratur
- W. Krenkel (red.): Keramiske kompositmaterialer . Wiley-VCH, Weinheim 2003. ISBN 3-527-30529-7
- J. Kriegesmann (red.): DKG - tekniske keramiske materialer . HvB-Verlag, Ellerau 2005. ISBN 978-3-938595-00-8
- WJ Bartz (red.): Keramiske lejer, materialer - glidelejer og rullelejer - tætninger . Håndbog til tribologi og smøringsteknologi. Bind 12. Ekspert Verlag, Renningen 2003. ISBN 3-8169-2050-0
Referencer
- ↑ Narottam P. Bansal, Jacques Lamon: Keramisk Matrix Composites Materialer, Modellering og teknologi . John Wiley & Sons, 2014, ISBN 978-1-118-83289-9 , pp. XV ( begrænset forhåndsvisning i Google Bogsøgning).
- Kun M. Kunz, "Ceramic Matrix Composites" , cfi / rapport fra DKG, bind 49, nr. 1, 1992, s. 18
- ↑ M. Kunz: Modstandsdygtighed over for keramiske fiberkompositter . Afhandling ved universitetet i Karlsruhe, Shaker Verlag , Aachen, 1996.
- ↑ A. Mühlratzer, M. Leuchs: Anvendelser af ikke-Oxide CMCs , fra: Højtemperatur Keramisk Matrix Composites .., Ed W. Krenkel et al, Wiley-VCH, Weinheim, 2001 ISBN 3-527-30320-0 , S. 288
- ^ H. Pfeiffer: Keramisk kropsklappe til X-38 og CRV . 2. internationale symposium om atmosfæriske genindtrædenskøretøjer og -systemer, Arcachon, Frankrig, marts 2001
- ^ H. Pfeiffer, K. Peetz: Hel -keramisk kropsklappe kvalificeret til rumflyvning på X-38 . 53. internationale astronautiske kongres, Houston, Texas, USA, oktober 2002, papir IAF-02-I.6.b.01
- ↑ H. Lange, M. Dogigli, M. Bickel: Keramiske Fasteners for høje temperaturer . 5. internationale konference om sammenføjning: keramik, glas og metal, Jena, maj 1997, DVS rapporterer bind 184, Deutscher Verlag für Schweißtechnik, s. 55, ISBN 3-87155-489-8
- ↑ M. Dogigli, H. Weihs, K. Wildenrotter, H. Lange: Ny High-Temperature Ceramic Bearing til rumfartøjer . 51. internationale astronautiske kongres, Rio de Janeiro, Brasilien, oktober 2000, papir IAF-00-I.3.04
- ↑ N. Miriyala, J. Kimmel, J. Price, H. Eaton, G. Linsey, E. Sun: Evalueringen af CFCC liner Efter feltforsøg i en gasturbine - III . ASME Turbo Expo Land, Sea & Air, Amsterdam, juni 2002, Paper GT-2002-30585
- ^ KL More, PF Tortorelli, LR Walker, JB Kimmel, N. Miriyala, JR Price, HE Eaton, EY Sun, GD Linsey: Evaluering af miljøbarrierebelægninger på keramiske matrixkompositter efter motor- og laboratorieeksponeringer . ASME Turbo Expo Land, Sea & Air, Amsterdam, juni 2002, Paper GT-2002-30630
- ↑ WEC Pritzkow: Keramisk plade, et materiale til de højeste krav . cfi specialudgave til DKG-DGM Symposium High Performance Ceramics 2005, W. Krenkel (red.), ISSN 0173-9913 , s. 40
- ↑ WEC Pritzkow: Oxid-fiber-forstærket keramik . cfi / Ber. DKG 85 (2008) Nr. 12, s.E1
- ↑ a b K. Gaffal, A.-K. Usbeck, W. Prechtl: Nye materialer muliggør innovative pumpekoncepter til pumpning af fødevand i kedelsystemer . VDI rapporter nr. 1331, VDI-Verlag, Düsseldorf, 1997, s. 275
- ↑ W. Kochanowski, P. Tillack: Nye pumpe bærende materialer forhindre beskadigelse rørformet hylster pumper . VDI rapporter nr. 1421, VDI-Verlag, Düsseldorf, 1998, s. 227
- ↑ JL Bozet, M. Nelis, M. Leuchs, M. Bickel: Tribologi i flydende ilt af SiC / SiC keramiske matrixkompositter i forbindelse med design af hydrostatisk leje . Proceedings of the 9.th European Space Mechanisms & Tribology Symposium (ESMAT), Liège, Belgium, september 2001, ESA Document SP-480, s.35
- ↑ M. Bickel, M. Leuchs, H. Lange, M. Nelis, JL Bozet: Keramiske journallejer i kryogene turbopumper . 4. internationale konference om affyringsteknologi - Space Launcher Liquid Propulsion, Liège, Belgien, december 2002, papir # 129
- ↑ P. Boullon, G. Habarou, PC Spriet, JL Lecordix, GC Ojard, GD Linsey, DT Feindel: Karakterisering og dysetesten oplevelsen af en Self Sealing Keramisk Matrix Composite til Gas Turbine Applications , ASME Turbo Expo Land, Sea & Air, Amsterdam, juni 2002, papir GT-2002-30458
- ^ B. Riccardi, L. Giancarli, A. Hasegawa, Y. Katoh, A. Kohyama, RH Jones, LL Snead: Spørgsmål og fremskridt inden for SiC f / SiC Composite-udvikling til fusionsreaktorer . Journal of Nuclear Materials, bind 329-333, 2004, s.56
- ↑ a b c d W. Krenkel: Anvendelsespotentialer for fiberarmeret C / C-SiC-keramik , i lit .: W. Krenkel, 2003, s. 220